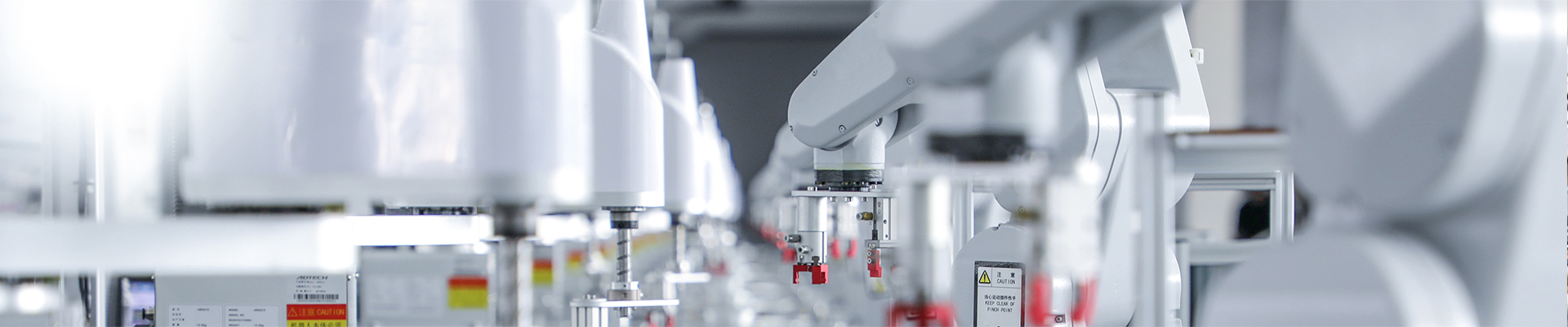
Análisis exhaustivo de las características técnicas y el rendimiento del transformador de soldadura por resistencia.
2025-03-22 14:52Los transformadores de soldadura por resistencia ofrecen alta eficiencia, alta velocidad, soldadura robusta, reducen los costos de soldadura y son adecuados para soldar diversos materiales. Son aptos para alimentación de CA con una frecuencia nominal de 50-60 Hz y una tensión inferior a 1000 V. Se utilizan principalmente en máquinas de soldadura por puntos, de costura y a tope.
I. Características técnicas
(1) Características del proceso de alta corriente y bajo voltaje
La soldadura por resistencia utiliza calor resistivo como fuente de calor. La principal característica técnica del transformador de la máquina de soldar es el uso de alta corriente (2000-40000 A) combinada con soldadura de bajo voltaje. Dado que el valor de resistencia de la pieza de trabajo suele ser inferior a 100 μΩ, se requiere generar suficiente calor mediante una corriente ultraalta para lograr una soldadura eficaz.
(2) Sistema de control de alta potencia
La capacidad del transformador inversor de soldadura suele ser superior a 50 kVA, y se adopta un diseño especial de bobinado (estructura de una o dos espiras) para controlar la potencia de salida mediante el ajuste del número de espiras del devanado primario. Si bien este diseño simplifica la estructura del transformador inversor de soldadura, también limita la flexibilidad de la regulación de potencia.
(3) Características de funcionamiento con carga no continua
El circuito de soldadura adopta un diseño único de precierre: antes de encender el transformador de soldadura mfdc, se precompletan la sujeción de la pieza y el cierre del circuito. Este modo de trabajo elimina el consumo de energía en vacío (excepto en el proceso de soldadura a tope por chispa), y la carga y descarga, el posicionamiento, el preprensado y otros procesos del ciclo de soldadura se completan con la máquina apagada.
2. Ventajas técnicas
(1) Garantía de calidad metalúrgica
El proceso de formación de pepitas está completamente envuelto por el anillo de metal plástico, que logra el aislamiento físico de la zona de fusión y el aire, simplifica efectivamente el proceso de reacción metalúrgica y asegura la estabilidad de la calidad de la soldadura.
(2) Excelente control de la zona afectada por el calor
Las características de calentamiento concentrado (tiempo de calentamiento ≤ 0,1 segundos) controlan el rango de la zona afectada por el calor a 0,5-2 mm, lo que reduce significativamente la tensión residual y la deformación de la soldadura. La mayoría de las piezas no requieren corrección ni tratamiento térmico después de la soldadura.
(3) Excelente eficiencia económica
No se requiere material de soldadura (alambre, varilla, gas de protección, etc.), y el coste de soldadura se reduce aproximadamente un 40 % en comparación con el proceso tradicional. El equipo cuenta con un alto grado de automatización y el volumen de soldadura por turno puede alcanzar entre 800 y 1200 piezas.
(4) Ventajas medioambientales
Durante todo el proceso no se producen llamas abiertas ni emisiones de humo, y el nivel de ruido es ≤ 65 dB (A), lo que cumple con las normas de protección ambiental industrial. El transformador para máquina de soldar es especialmente adecuado para la integración en líneas de producción automatizadas y permite la operación sincronizada de múltiples procesos.
3. Limitaciones técnicas
(1) Desafíos de la inspección de calidad
Aún no se ha establecido un sistema de ensayos no destructivos consolidado. Actualmente, la calidad se garantiza principalmente mediante ensayos destructivos y la monitorización de procesos, lo que dificulta el control de los mismos.
(2) Restricciones de desempeño conjunto
Las uniones traslapadas con soldadura por puntos tienen defectos estructurales inherentes: el ángulo alrededor de la pepita de soldadura provoca una concentración de tensión, lo que hace que la resistencia a la tracción decaiga en aproximadamente un 15-20%, y la vida útil por fatiga es solo del 60-70% de la de las soldaduras continuas.
(3) Costos de operación y mantenimiento de equipos
La inversión inicial en equipos de alta potencia (configuración típica de 400 kVA) es elevada, y las máquinas de soldadura monofásicas de CA son propensas a causar desequilibrios en la red. El sistema servo de precisión aumenta la complejidad del mantenimiento, y el costo de reemplazo de componentes clave (como los módulos de tiristores) supera el 25 % del precio total del equipo.
4. Dirección de la evolución de la tecnología
La nueva generación de equipos de soldadura por resistencia está rompiendo las limitaciones existentes mediante las siguientes innovaciones tecnológicas:
Desarrollo de un sistema de monitorización de calidad en tiempo real basado en imágenes térmicas infrarrojas
Introducción de la tecnología de corriente pulsada para optimizar la microestructura articular
Uso de tecnología de rectificación trifásica para mejorar la compatibilidad con la red
Diseño de unidades de potencia modulares para reducir costos de mantenimiento
Estas mejoras han permitido que la soldadura por resistencia muestre perspectivas de aplicación más amplias en campos emergentes, como los paquetes de baterías para vehículos de nueva energía y la fabricación de piezas de precisión aeroespaciales.